Solutions for the steel industry
ABC&I´s products in the field of NOx-reduction encompass three different methodologies. The first alternative uses a mathematical modelling method in which combustion-controlling parameters are optimised in such a way that the NOx-formation is steered to a minimum level. Used mathematical tools are CFD – and/or multivariate analysis. A typical optimisation normally leads to a NOx reduction between 10-30% depending on the complexity in the combustional system. The higher the complexity, the higher potential of NOx-reduction. Constraints are CO-level and furnace time/temperature profile for the processed steel quality.
The second and third methodologies are building on chemical NOx-reduction by means of a nitrogen based reduction agent. Used technologies are SNCR- Selective Non Cathalytic NOx-Reduction or SCR- systems (Selective Cathalytic NOx-Reduction). Due to lack of cost efficiency, SCR has so far not been used in the context of steel production in ABC&I led projects.
NOx-reduction in the steel industry are complex. Requirements are demanding not only on reduction in NOx but also in respect to the furnace and the conditions inside the furnace. Elimination of the potential risk of enhanced CO-emissions as well as inter activated formation of N2O are other important requirements.
The internal furnace exposure from added chemicals requires high technology solutions. Well proven design, advanced construction materials together with an intelligent control system have successfully been used in reference projects during the last decade of years.
Environmental benefits
Lessened NOx-emissions to atmosphere are lowering negative impacts on the receiving eco system. The most pronounced are:
- Acid rain
- Ozone formation on ground level
- Nitrogen outlet to the marine eco system
Lower NOx-emissions reduces negative influence on humans as well as on other living species
NOx-formation in the furnace burner zone
NOx sources are:
a. Thermal NOx-dominating at high temperatures in the burner zone
b. Fuel nitrogen NOx - stemming from the nitrogen content in the fuel
c. Prompt NOx - small contribution in the context of steel production
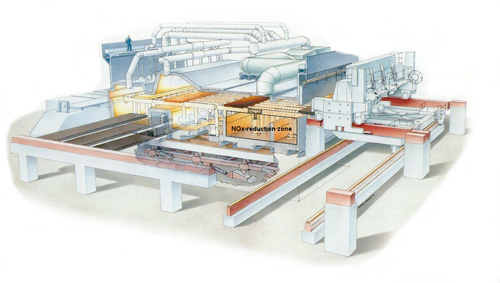
Thermal NOx-formation and steel production constraints
Gas temperatures in the flame zones of the burners are normally 1500ºC - 2300ºC, in oxyfuel applications even higher. In order to accomplish a full temperature processing profile of the steel material, the furnace gas needs to exceed temperatures in the interwall of 1100ºC - 1400ºC as a typical case.
Used deNOx chemicals
The most potent reduction agents for the NOx-reduction are normally nitrogen based. For best performance the most appropriate chemical should be used. The system design together with the selected chemical for NOx-reduction must satisfy various types of criteria. Criteria which will be depending on the specific operational conditions in the furnace/burner zones. ABC&I provides deNOx- reduction options in respect to all commercial available reduction agents. Based on the properties of the steel production system, the most appropriate reduction agent is selected. ABC&I have vast experience from excisting reference plants where different chemicals have shown to produce the most optimal results in different types of steel production plants.
Investment costs- Non catalytic NOx-reduction
Investment costs are comparatively low in respect to other measures against emissions such as dust or technologies based on catalysis or scrubber absorption.
Chemical costs
Cost of chemicals is an important factor in reducing NOx-emissions. Selecting the best technology design is much a question of chemical use efficiency. A low technology based NOx-reduction could require twice the quantity of the chemicals for a specific set level of NOx-emission.
Potential impact on the steel producing system
Used reduction agents are potent chemicals and must be treated in accordance with normal chemical processing procedures. The equipments used for NOx-reduction must have high enough standard in respect to chemical risk exposure as well as resist destructive forces from high temperatures (ca 1000ºC) and a corrosive flue gas. The NOx-reducing equipments must also stand the aggressive environment after many years of operation, giving a safe and reliable operation in respect to NOx-reduction and to the steel production plant itself.
The most appropriate technical design for the reduction system must incorporate type of steel mill furnace and requirements put on NOx, chemical-slipp, operational costs etc. Number and the divercity of deNOx projects delivered to the steel industry makes the ABC&I company to a leading supplier in this highly specialized field.
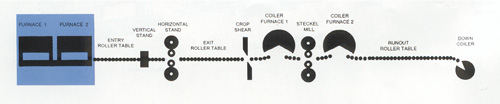
|